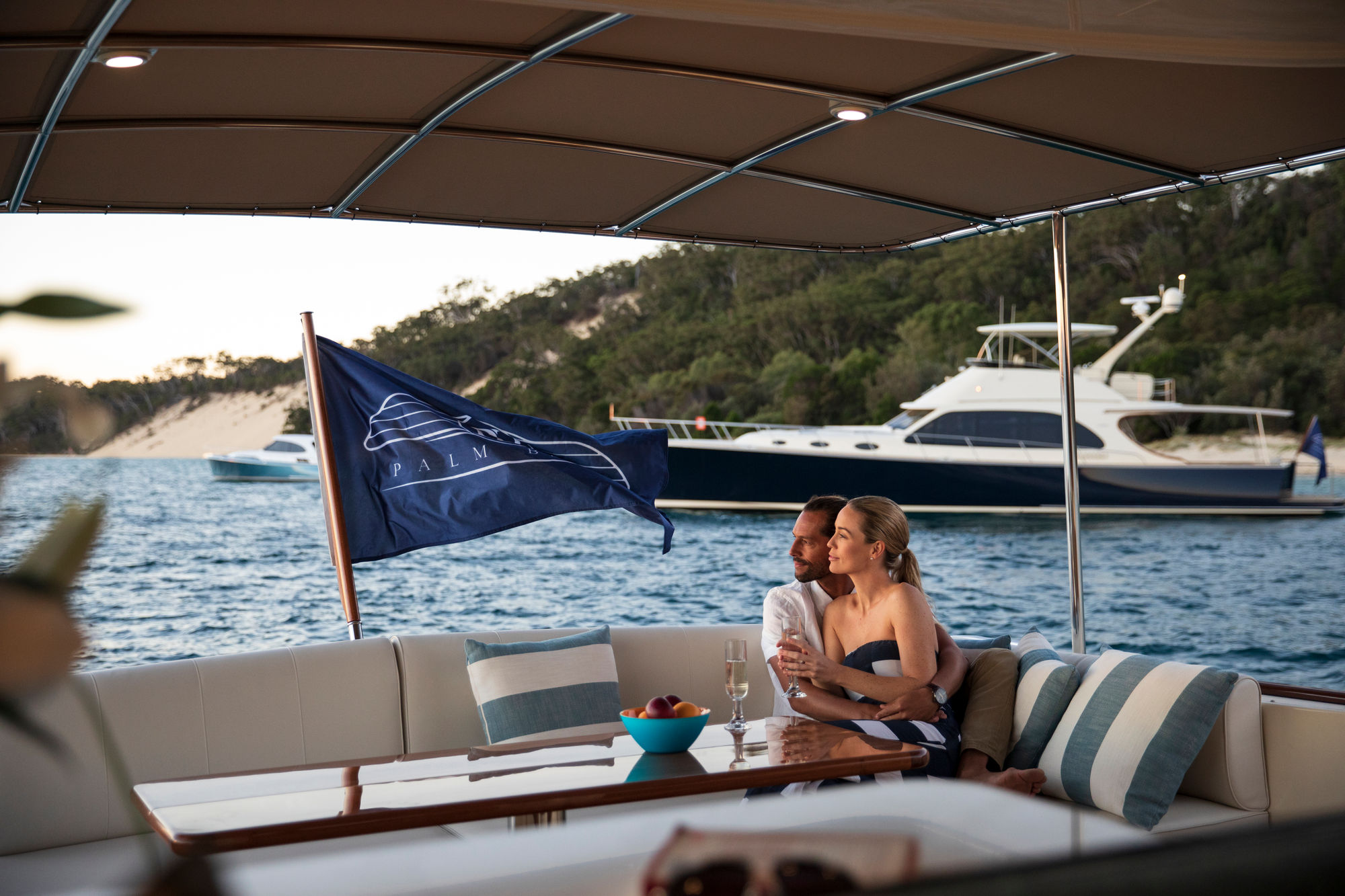
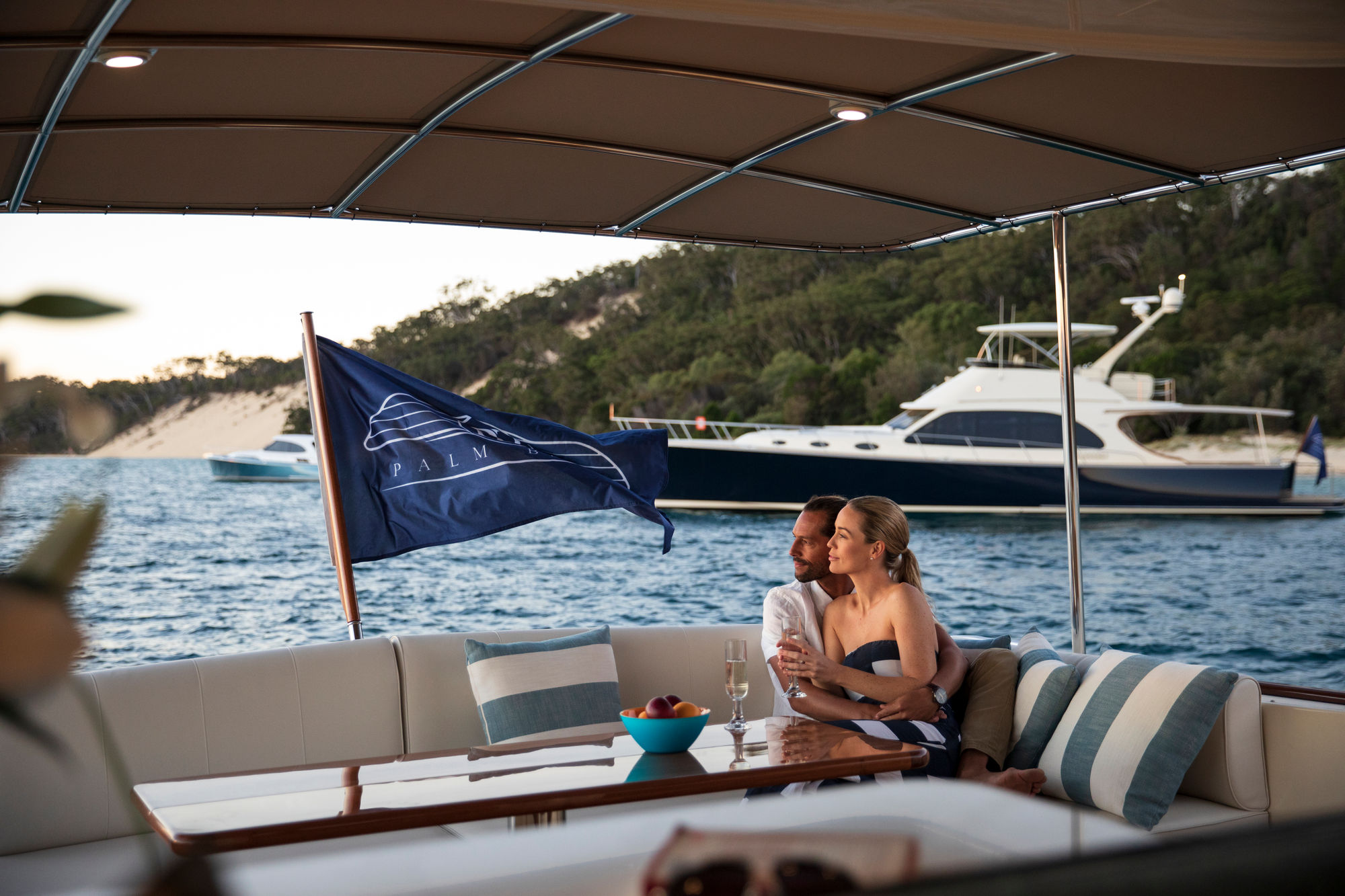
SUPERIOR CRAFTSMANSHIP; UNMATCHED CUSTOMIZATION
The customization process begins with understanding your personal preferences and requirements. We offer an extensive selection of options for materials, finishes, and fittings, enabling you to create a space that truly reflects your personality. Our experienced designers and craftsmen are dedicated to achieving the highest standards of quality and artisanry, ensuring that every element of your yacht is meticulously tailored to your specifications. The result is a level of bespoke yachting that is nearly unheard of outside the upper realms of superyachts.
COMMITMENT TO EXCELLENCE
From the initial design phase to the final touches, our dedicated team works tirelessly to bring your vision to life. With a commitment to excellence and a passion for innovation, we ensure that your yacht not only meets but exceeds every expectation. Experience the ultimate in luxury and personalization with Palm Beach Motor Yachts, where your dream yacht becomes a reality.
ARTISTRY IN EVERY DETAIL
Discover the exquisite craftsmanship and personalized touches that define our yachts, showcasing the bespoke beauty of each unique creation.
INTEGRATED DESIGN, BUILD, AND SALES
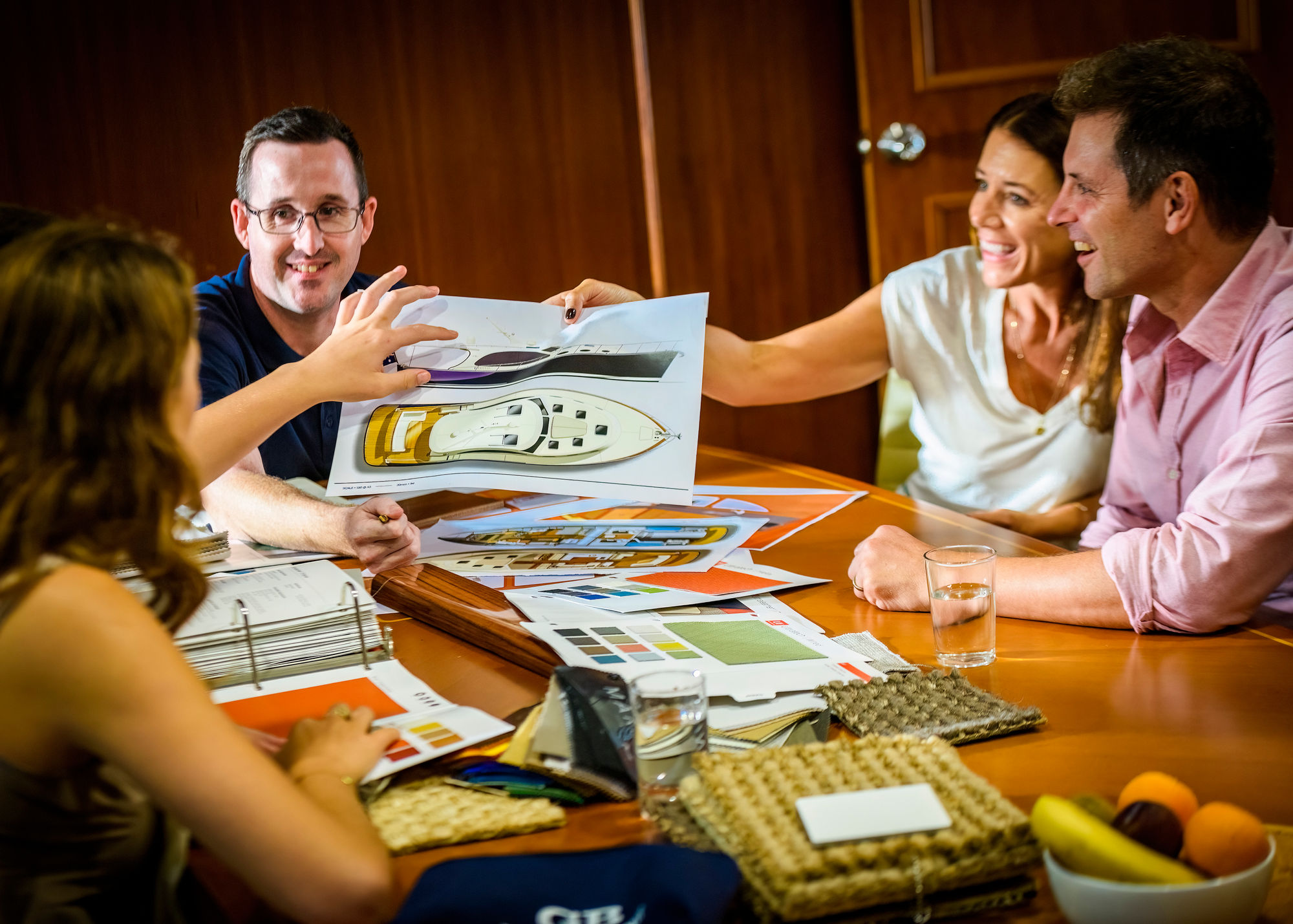
PALM BEACH MOTOR YACHTS WARRANTY
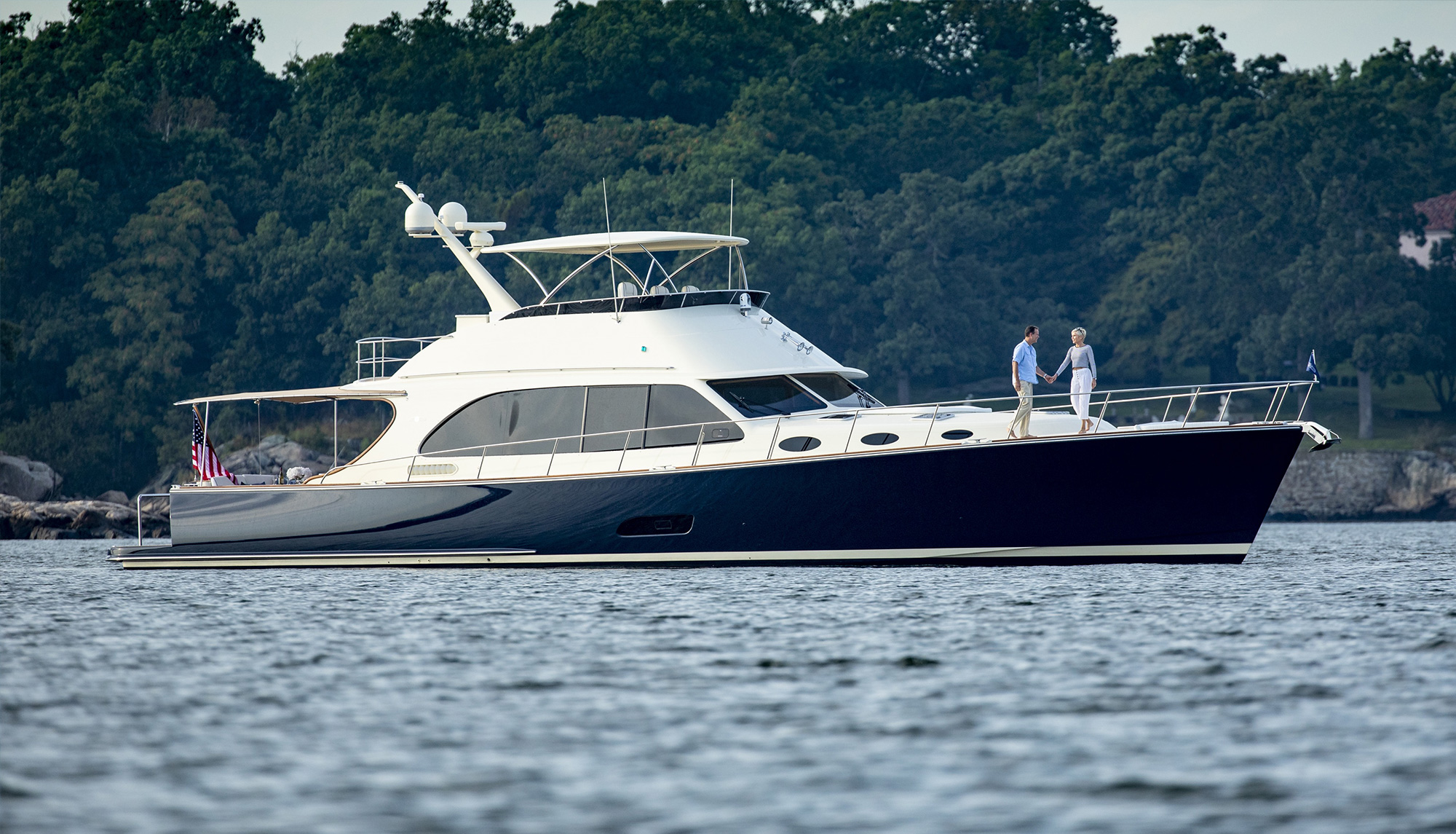
NEW MODELS
The hull and deck of your yacht come with a five-year structural warranty and the engines are also supplied with extended warranties of five years. Any third-party components are covered by vendor warranties that we have approved, and we can discuss these with you during your build design.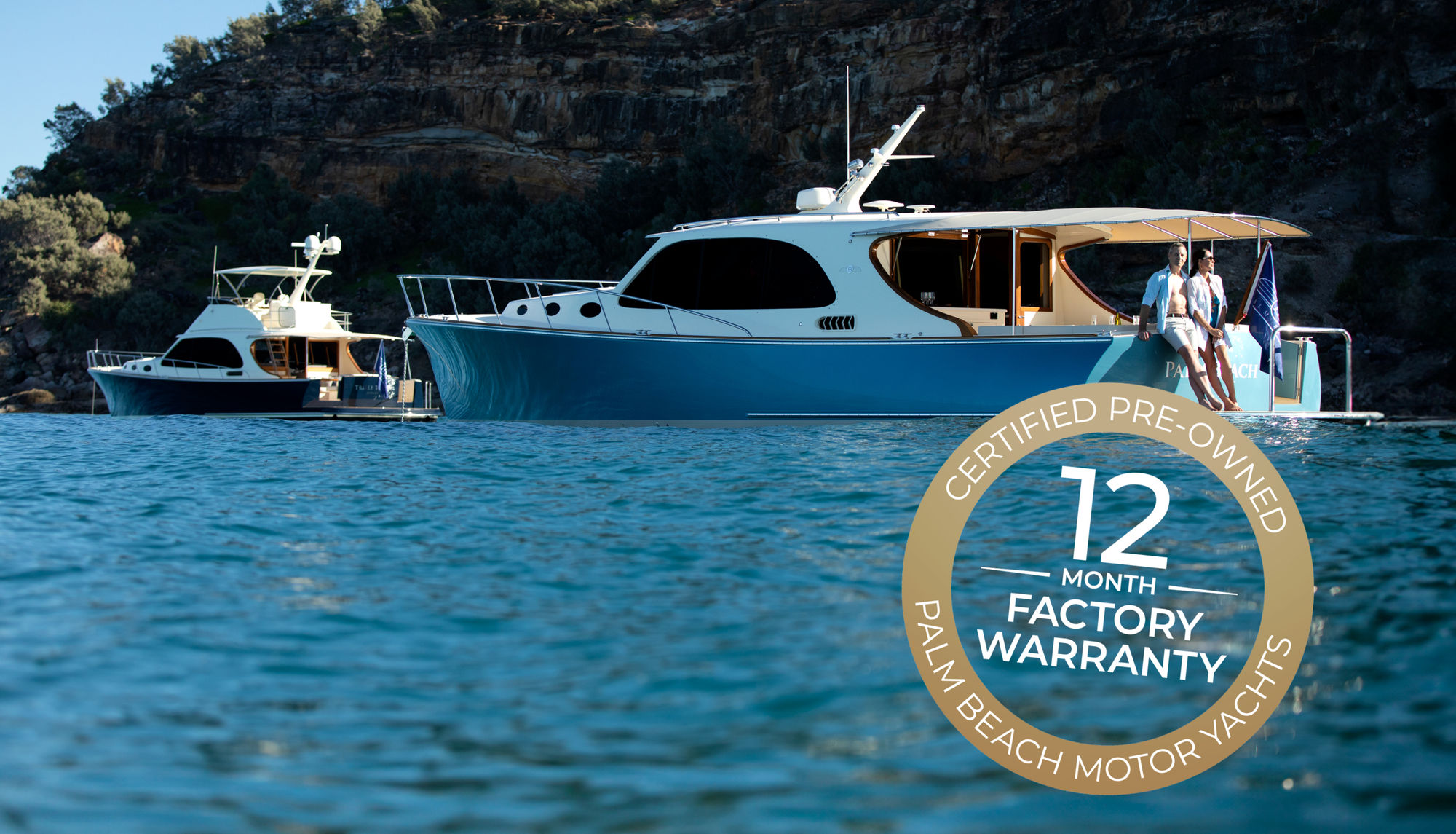
PRE-OWNED
Our Certified Pre-Owned Warranty highlights our dedication to quality and client relationships. This free 12-month warranty ensures inspected and detailed yachts are protected against defects, maintaining our craftsmanship's integrity. Enjoy reliable support and peace of mind with Palm Beach Motor Yachts.THE PALM BEACH MOTOR YACHTS PERKS
SINGLE POINT OF CONTACT
Every Palm Beach client is assigned a single point of contact to ensure seamless communication and coordination throughout the entire process, ensuring your needs are met with personalized attention and efficiency.24/7 ASSISTANCE
Experience peace of mind with our 24/7 assistance, offering round-the-clock support and immediate responses to any concerns or emergencies.EXPERTS AROUND THE WORLD
Benefit from our extensive network of experts located across the globe, providing local knowledge, specialized skills, and prompt service wherever you are.